How AI Helped Acme Manufacturing Win Back 12 Hours a Week With Time Savings and Efficiency
Acme Manufacturing faced a chronic challenge: an ever-tightening schedule and a growing demand for faster production rates without sacrificing product quality. Amid intense competition and rising labor costs, the company sought innovative solutions for reclaiming lost time and improving overall operational efficiency. In this pursuit, Acme Manufacturing turned to artificial intelligence (AI). By integrating AI systems into its production lines, maintenance routines, quality control processes, and supply chain management, the firm not only boosted its productivity but also achieved a remarkable reduction in downtime. The transformative changes enabled Acme Manufacturing to save 12 hours every week—a figure that translates directly into improved throughput, reduced operational costs, and enhanced customer experience.
This comprehensive article explores the myriad ways in which AI has revolutionized time management in manufacturing. It examines key benefits such as enhanced efficiency, reduced downtime, and improved labor cost management. Detailed discussions about AI-powered predictive maintenance, process optimization, quality control measures, and supply chain innovations elaborate on how each element contributes to drastic time savings. Real-world applications and measurable success stories, including specific data from Acme’s AI implementation, provide compelling evidence for the adoption of AI technologies in manufacturing settings. For business leaders and manufacturing managers, understanding both the technical and operational dimensions of these AI solutions is vital for replicating similar successes in their organizations.
Furthermore, this article addresses common questions regarding AI integration, predictive maintenance, process optimization, and supply chain management, providing actionable steps and clear guidelines to help manufacturers harness artificial intelligence to reclaim valuable time. The insights presented here are designed for small to mid-sized businesses aiming to improve efficiency and ensure that technology ultimately serves to enhance, rather than complicate, daily operations. By strategically embedding AI across various facets of the organization, companies can expect not only immediate time savings but also long-term competitive advantages, improved product quality, and better resource allocation.
As the manufacturing landscape continues to evolve, the role of AI becomes increasingly indispensable. This transformation is not just about automating processes; it’s about making smarter decisions, predicting issues before they occur, and optimizing every step of the manufacturing process. The following sections detail the key benefits, strategies, and outcomes of being an industry leader through AI implementation.
By leveraging advanced data analytics and machine learning, companies can enhance productivity and reduce downtime significantly. Moreover, understanding ai implementation strategies for businesses is crucial for tailoring solutions that align with specific operational needs. As organizations embrace these innovative technologies, they position themselves not only for immediate gains but also for sustainable growth in a competitive marketplace.
To fully capitalize on the advantages offered by AI, companies must foster a culture of continuous learning and adaptation among their workforce. This proactive approach enables teams to innovate and refine AI applications, ensuring they consistently maximize business impact with AI. Ultimately, organizations that prioritize AI integration are better equipped to navigate challenges and seize new opportunities in their respective industries.
What Are the Key Benefits of AI Time Savings in Manufacturing?
Manufacturing enterprises worldwide are witnessing revolutionary changes as AI-enhanced systems streamline operations and dramatically reduce time wastage. One of the primary benefits is the significant improvement in efficiency and productivity across production lines. AI technologies, when integrated into manufacturing processes, offer real-time analytics, advanced process controls, and data-driven decision support that collectively lead to informed decisions. Manufacturers see enhanced throughput due to quicker response times to operational changes and a reduction in manual errors.
How Does AI Improve Manufacturing Efficiency and Productivity?
AI continuously monitors and analyzes production processes to identify inefficiencies and recommend adjustments to boost productivity. It leverages machine learning algorithms to process complex datasets from machine sensors and control systems. For example, by detecting subtle performance variations, AI can automatically adjust process parameters to maintain optimal productivity levels. Real-time monitoring means any deviation from the norm is swiftly corrected, preventing lengthy disruptions. This rapid responsiveness not only improves production flow but also minimizes rework costs and manual oversight, all of which play a critical role in maximizing operational efficiency.
In What Ways Does AI Reduce Downtime and Labor Costs?
AI contributes to downtime reduction through predictive capabilities that preempt equipment failures. It continuously learns from historical machine data and operational trends to forecast when a machine is likely to fail or require maintenance. These predictive insights enable preemptive repairs and scheduling adjustments that significantly minimize unplanned downtime. By automating routine inspections and leveraging self-correcting control systems, AI ensures that labor input shifts from reactive maintenance to proactive optimization strategies. As a result, manufacturers experience fewer interruptions, better resource allocation, and an overall reduction in labor costs—a vital advantage in an industry with tight margins.
Why Is Time Savings Critical for Manufacturing Operations?
Time is a critical resource in manufacturing, with every minute of downtime directly affecting production output and profitability. In industries where rapid-cycle production is the norm, even small time savings can lead to substantial increases in overall output. Moreover, as manufacturers face international competition, the speed at which products are delivered can be a decisive factor in customer satisfaction and market share. By cutting down machine idle times, enabling faster transitions between production batches, and enhancing supply chain responsiveness, manufacturers are better positioned to meet customer demands and improve their competitive edge in a fast-paced global market.
How Does AI-Powered Predictive Maintenance Save Time at Acme Manufacturing?
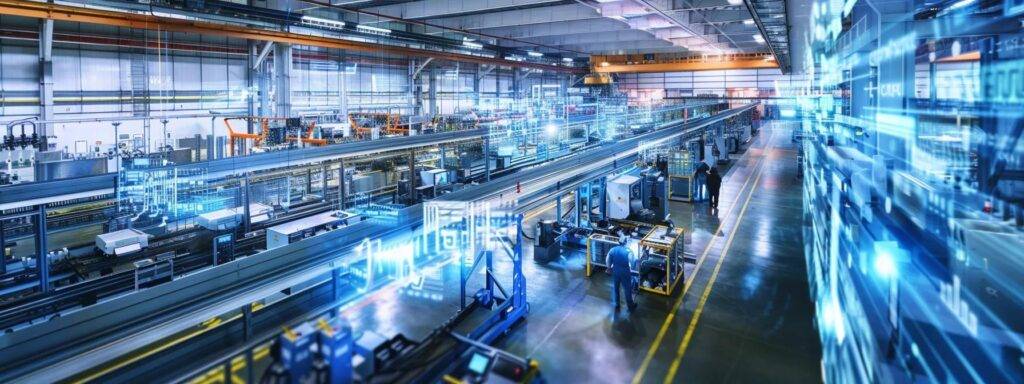
Predictive maintenance, empowered by AI, is a game-changing technology for modern manufacturing. It leverages sensor data and advanced algorithms to predict equipment failures before they occur, thereby avoiding costly unplanned downtime. At Acme Manufacturing, the implementation of AI-powered predictive maintenance has created a paradigm shift in how maintenance tasks are scheduled and executed, directly affecting overall operational efficiency.
What Is Predictive Maintenance and How Does AI Enable It?
Predictive maintenance uses AI algorithms to constantly analyze equipment condition through data gathered from sensors integrated into machinery. This continuous monitoring process captures parameters such as vibration, temperature, and sound, which are indicators of equipment health. AI then processes this data to detect patterns and predict maintenance needs before a breakdown occurs. In effect, predictive maintenance transforms the traditional reactive maintenance model into a proactive system where interventions are precisely timed to avoid production halts. With these capabilities, manufacturers can schedule repairs during planned downtime, ensuring uninterrupted production workflows.
How Does Predictive Maintenance Reduce Equipment Failures and Downtime?
By analyzing real-time and historical data, AI-driven predictive maintenance systems recognize early warning signs of potential equipment failures. This early detection allows for timely interventions, resulting in the prevention of sudden machine malfunctions. At Acme Manufacturing, this approach has led to a measurable decrease in equipment failures, thereby reducing the cumulative downtime experienced each week. The system’s ability to continuously learn and adjust to changing operating conditions further enhances its predictive accuracy. Consequently, maintenance teams can allocate resources more efficiently and ensure that critical equipment remains operational, culminating in fewer production interruptions and sustained manufacturing performance.
What Time Savings Did Acme Manufacturing Achieve Through Predictive Maintenance?
Acme Manufacturing reported a substantial reduction in downtime after deploying an AI-based predictive maintenance program. The technology enabled the company to schedule maintenance activities during planned downtimes and avoid unforeseen disruptions. As a result, Acme claimed a time savings of 12 hours per week—a significant achievement that translates into increased production capacity and improved responsiveness to market demands. This reduction in downtime not only enhances operational efficiency but also streamlines production planning and workforce allocation, providing the company with a competitive edge in its industry.
How Does AI-Driven Process Optimization Contribute to Time Savings?
AI-driven process optimization leverages advanced analytics and machine learning to meticulously evaluate and improve every facet of the production process. Through continuous monitoring, data gathering, and algorithmic adjustments, these AI systems identify production bottlenecks, streamline operations, and ultimately reduce cycle times. For manufacturers like Acme, process optimization means achieving faster production rates with enhanced precision and fewer errors.
What AI Technologies Are Used for Manufacturing Process Optimization?
A range of AI technologies plays a role in process optimization, including machine learning, computer vision, and advanced analytics. Machine learning models analyze complex datasets on production performance to predict optimal operating conditions. Computer vision systems monitor production lines in real time, detecting anomalies and ensuring quality control. Additionally, advanced analytics tools synthesize data from various stages of the production process to highlight inefficiencies and suggest process improvements. These integrated systems work synergistically to refine production methods, making the entire manufacturing process more efficient and responsive to live conditions.
How Does AI Identify and Eliminate Production Bottlenecks?
By continuously monitoring production data, AI systems track the flow of materials and the performance of each production line component. They are capable of identifying even minor deviations that indicate a bottleneck. Once a bottleneck is detected, the system provides actionable insights and recommendations to eliminate the obstruction. For instance, if a specific machine’s performance is lagging due to wear or configuration issues, AI analysis can trigger maintenance or temporary reallocation of tasks. This precise identification and resolution of issues allow production lines to maintain optimal speed, significantly reducing cycle times and ensuring that the entire process operates at peak efficiency.
What Are the Measurable Time and Cost Benefits of Process Optimization?
Process optimization driven by AI has tangible, measurable benefits. Manufacturers have observed improvements such as a 15–20% reduction in production cycle times and significant cost savings from minimized downtime and reduced waste. At Acme Manufacturing, the integration of process optimization tools not only shortened cycle times but also decreased the operational costs associated with rework and maintenance. These time and cost benefits are critical in a competitive landscape where efficiency directly correlates with profitability. The cumulative effect of minute improvements across the production process can result in considerable advantages, empowering manufacturers to meet demand more effectively and improve overall return on investment (ROI).
How Is AI Used for Quality Control and Inspection to Save Time?
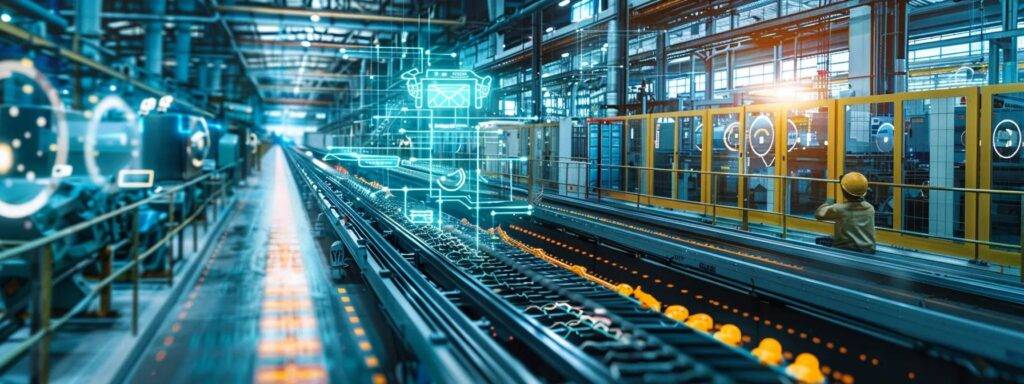
Quality control and inspection are traditionally labor-intensive tasks in manufacturing, but AI revolutionizes these processes by automating defect detection and inspection procedures. With the capacity to analyze visual data and other sensory inputs at unprecedented speeds, AI-based quality control systems significantly reduce inspection times while enhancing accuracy. This not only leads to better product quality but also saves valuable production time.
What AI Methods Detect Defects Faster Than Manual Inspection?
Computer vision combined with deep learning models is at the core of AI-driven quality control. These systems analyze high-resolution images of products in real time, identifying defects that might be overlooked by the human eye. Techniques such as convolutional neural networks (CNNs) enable precise categorization of visual anomalies and ensure that each product meets production standards without the delay of manual inspection. In addition, sensor-based methods often integrate with these vision systems to monitor dimensions, tolerances, and material properties, ensuring comprehensive quality assurance with minimal delay. This rapid, automated inspection process dramatically outpaces traditional methods, resulting in faster throughput and fewer rejections.
How Does AI Improve Product Quality While Reducing Inspection Time?
AI enhances product quality by ensuring consistency throughout the inspection process. Its ability to detect even the slightest defects ensures that only products meeting strict quality standards move forward in the production process. This precise quality control minimizes the time spent on additional re-inspections and decreases the incidence of returns and defects reaching customers. For instance, by incorporating real-time feedback into the production process, manufacturers can make on-the-spot adjustments that prevent recurring quality issues. As a result, overall inspection time is reduced, and product excellence is maintained, helping companies solidify their market reputation for high-quality manufacturing.
What Impact Does AI Quality Control Have on Overall Manufacturing Efficiency?
The integration of AI in quality control directly contributes to a smoother production flow and enhanced manufacturing efficiency. With faster inspection times and lower error rates, fewer production pauses and material wastage occur, enabling the assembly lines to operate continuously. The predictive possible analysis and instant feedback provided by these systems empower companies to refine their processes on the fly—a benefit that not only saves time but also results in significant cost savings. Across the manufacturing sector, AI-driven quality control is recognized as a vital tool for maintaining consistent quality while ensuring the full utilization of production capacity.
What Role Does AI Play in Supply Chain Management to Save Time?
AI is not only transforming manufacturing itself but also the broader supply chain processes that support production. From demand forecasting to inventory management and logistics, AI systems optimize each segment, reducing lead times and ensuring that materials and finished products are always in the right place at the right time. These improvements drastically cut down on delays and inefficiencies that can affect overall production schedules.
How Does AI Forecast Demand and Optimize Inventory Levels?
Advanced AI algorithms analyze historical sales data, market trends, and external factors such as seasonality and economic indicators to forecast demand with remarkable accuracy. This predictive capability enables supply chain managers to determine the optimal inventory levels required to meet future demand without overstocking or running out of critical materials. As a result, manufacturers experience fewer production delays caused by shortages or excess inventory—both common sources of time waste. Precise demand forecasting and inventory optimization ensure that resources are allocated efficiently, leading to smoother production cycles and a more resilient supply chain.
In What Ways Does AI Streamline Logistics and Delivery Processes?
AI streamlines logistics by automating route planning, shipment scheduling, and delivery tracking. Machine learning models can analyze real-time traffic data, weather conditions, and other logistical variables to determine the fastest and most efficient delivery routes. In addition, AI-driven systems coordinate with warehouse management systems to ensure that shipments are processed, packed, and dispatched without delays. This comprehensive approach to logistics management minimizes delivery times and enhances the overall flow of materials from suppliers to manufacturing facilities, ultimately improving production scheduling and reducing delays due to transportation inefficiencies.
How Does Supply Chain AI Reduce Delays and Improve Resource Allocation?
By integrating artificial intelligence across supply chain operations, companies are better equipped to monitor every step of the process. AI-enabled dashboards aggregate data from various sources to provide real-time insights into bottlenecks and delays. This holistic view allows supply chain managers to reassign resources and adjust strategies quickly to address any emerging issues. The improved interconnectivity between different stages of the supply chain means that delays are minimized, and resources—both human and material—are utilized more effectively. Manufacturers gain a competitive edge by consistently maintaining the right balance between supply and demand, which directly translates into shorter production lead times and enhanced time savings across the entire operation.
What Are the Specific Results of Acme Manufacturing’s AI Implementation?
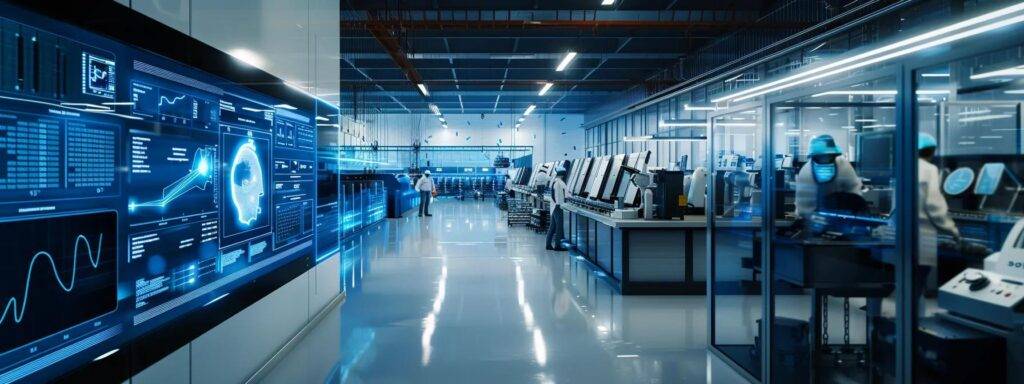
Acme Manufacturing’s strategic adoption of AI solutions has yielded impressive, quantifiable results that underline the transformative impact of technology on manufacturing efficiency. The company not only recorded a saving of 12 hours per week but also noted improvements in overall production output and a significant reduction in operational downtime. Through detailed analysis and continuous monitoring, Acme has established an AI framework that can be scaled and adapted to further optimize manufacturing processes.
How Did Acme Manufacturing Implement AI Solutions Across Operations?
Acme Manufacturing implemented AI solutions by integrating systems across various operational dimensions including predictive maintenance, process optimization, quality control, and supply chain management. The company collaborated with AI experts to tailor algorithms to its specific production needs, ensuring that every integration was data-driven and aligned with operational goals. By investing in sensor networks and real-time data analytics, Acme created a feedback loop that allowed immediate adjustments to production parameters. This seamless integration across departments ensured that improvements in one area supported enhancements in others, creating a synergistic effect that maximized the overall time savings.
What Challenges Were Overcome to Achieve 12 Hours a Week Saved?
During the transition to AI-driven operations, Acme Manufacturing encountered several challenges, including system integration complexities, data interoperability issues, and the need for staff training on new technologies. The company addressed these challenges by investing in robust IT infrastructure, partnering with technology providers for seamless system integration, and conducting comprehensive training sessions for employees. Resistance to change was mitigated through clear communication of the benefits and a trial period that demonstrated tangible improvements. Overcoming these operational hurdles ultimately resulted in the consistent saving of 12 hours of production time per week, validating the strategic benefits of AI in a real-world manufacturing setting.
What Are the Long-Term Benefits and ROI of AI at Acme Manufacturing?
The long-term benefits of Acme’s artificial intelligence implementation extend far beyond the immediate time savings. The company has experienced a sustained reduction in maintenance costs, increased product quality, and improved supply chain reliability. With a significant return on investment (ROI) realized through lower labor costs and higher production volumes, Acme is now positioned to reinvest these savings into further technological enhancements and innovation initiatives. Additionally, the integration of AI has bolstered employee satisfaction, as staff members are now empowered to focus on strategic tasks rather than routine maintenance and inspection, ultimately leading to a more innovative and engaged workforce.
How Can Other Manufacturers Achieve Similar Time Savings With AI?
The success of Acme Manufacturing serves as an inspiring blueprint for other manufacturers aiming to achieve similar time savings and operational efficiencies through AI. By carefully planning and executing a tailored AI strategy, manufacturers can overcome system integration challenges, streamline production, and significantly reduce downtime. The experience of Acme highlights the importance of a phased implementation plan, robust training programs, and continuous evaluation of AI-driven processes to ensure sustainable improvements.
What Steps Should Manufacturers Take to Start Using AI for Time Savings?
Manufacturers looking to incorporate AI should begin with a comprehensive assessment of their current operations to identify areas with the greatest potential for efficiency improvements. This involves auditing existing processes, collecting relevant operational data, and consulting with technology experts to determine the most appropriate AI solutions. A pilot program is recommended to test AI capabilities in a controlled environment before full-scale deployment. Additionally, investing in modern sensor networks, upgrading IT infrastructure, and ensuring seamless integration between AI systems and existing enterprise resource planning (ERP) software are essential steps. By following these recommendations, manufacturers can pave the way toward substantial time and cost savings.
Which AI Solutions Are Most Effective for Different Manufacturing Needs?
Different manufacturing challenges require targeted AI solutions. For instance, predictive maintenance systems are highly effective in reducing unplanned downtime by forecasting equipment failures, while AI-powered process optimization platforms are best suited for eliminating production bottlenecks. Quality control can benefit significantly from computer vision systems that rapidly detect defects, and supply chain management is drastically improved through advanced forecasting algorithms. Manufacturers should evaluate their unique challenges and select AI tools that align with their operational priorities. In many cases, layered solutions that integrate multiple AI technologies provide a comprehensive approach, addressing problems from multiple angles and maximizing overall automation.
How Can Companies Measure and Track AI-Driven Time Savings?
To ensure the effectiveness of AI implementations, companies must establish clear performance metrics and continuously track key performance indicators (KPIs). Time savings can be measured by comparing production cycle times, the frequency of equipment failures, and the duration of quality inspections before and after AI adoption. Companies can also use dashboards that integrate data from various AI systems to monitor real-time improvements. An effective tracking method involves setting up periodic assessments to verify that the AI systems continue to operate at optimal efficiency and to promptly address any emerging issues. Through regular evaluations, manufacturers can not only validate the initial ROI of AI investments but also identify additional improvement opportunities.
Detailed Lists of AI Benefits and Applications in Manufacturing
Below are several detailed lists, each outlining crucial AI applications within manufacturing and the specific benefits they deliver.
1. Top 7 AI-Driven Improvements in Manufacturing Efficiency
- Predictive Analytics – Reduced Downtime and Preemptive Repairs Predictive analytics use historical and real-time data to identify potential equipment failures, thus enabling maintenance teams to intervene before problems escalate. This approach significantly reduces unplanned downtime and increases overall machine availability, leading to smoother production processes and enhanced operational efficiency.
- Real-Time Analytics – Immediate Process Adjustments By continuously monitoring production data, real-time analytics facilitate rapid adjustments to process variables. This immediate reaction to operational anomalies ensures that production lines always run at peak efficiency, minimizing waste and optimizing throughput in dynamic manufacturing environments.
- Automated Quality Control – Enhanced Defect Detection and Consistency AI-powered computer vision systems quickly identify product defects with far greater accuracy than manual inspections. This automation not only speeds up the inspection process but also ensures a high level of quality consistency, reducing rework and customer returns.
- Robotic Process Automation (RPA) – Streamlined Repetitive Tasks RPA minimizes human intervention in repetitive tasks such as data entry, inventory management, and packaging. Automation of these tasks frees up employee time for more strategic activities that require human ingenuity, thereby improving overall productivity.
- Supply Chain Optimization – Improved Demand Forecasting AI algorithms enhance supply chain operations by accurately forecasting demand, optimizing stock levels, and streamlining logistics. This results in a more agile supply chain that can adapt to fluctuations, thereby reducing delays and ensuring the availability of critical components.
- Process Simulation and Digital Twins – Testing and Training Digital twins and process simulation tools provide a virtual replica of the production processes, enabling real-time testing of process changes without disrupting actual operations. This allows manufacturers to experiment with improvements and validate changes before implementing them on the factory floor.
- Energy Management Systems – Reducing Operational Costs AI-based energy management systems monitor and optimize energy consumption across production lines. By detecting inefficiencies and suggesting energy-saving measures, these systems reduce operational costs, contributing significantly to overall financial performance.
2. Key AI Technologies for Predictive Maintenance in Manufacturing
- Vibration Analysis – Early Fault Detection Vibration sensors combined with AI algorithms help detect early signs of mechanical wear and tear. These systems provide a proactive approach to maintenance by identifying potential issues before they become critical.
- Thermal Imaging – Monitoring Temperature Anomalies Thermal cameras integrated with AI analyze temperature patterns across equipment surfaces. This helps in detecting overheating or abnormal temperature spikes that may indicate underlying mechanical problems.
- Acoustic Monitoring – Sound Pattern Analysis Advanced acoustic sensors capture sound emissions from machinery, while AI models analyze these sounds to detect abnormalities. This method is particularly useful in identifying issues such as bearing failures or loose components.
- Oil Analysis – Monitoring Lubricant Properties Periodic oil sampling paired with AI diagnostics can identify contaminants or degradation in lubricant quality. Early detection of oil degradation helps in scheduling timely maintenance and avoiding critical engine failures.
- Ultrasonic Testing – Detecting Structural Flaws Ultrasonic sensors emit high-frequency sound waves to detect internal flaws in metal components. AI systems process the received signals to determine the presence of cracks or distortions, ensuring timely repairs.
- Current Monitoring – Electrical Efficiency Checks Monitoring the electrical current used by machines can provide insights into operational efficiency. AI systems analyze current fluctuations to detect any deviations that may indicate electrical issues or mechanical inefficiencies.
- Predictive Modeling – Synthesis of Multimodal Data By synthesizing data from various sources such as vibration, thermal, acoustic, and current sensors, predictive modeling provides a comprehensive overview of machine health. This holistic approach enhances the accuracy of predictions, ensuring that maintenance tasks are performed only when necessary.
3. Measurable Benefits from AI-Driven Process Optimization
- Cycle Time Reduction – Accelerated Production Processes AI-enabled process optimization has been shown to reduce production cycle times by up to 20%, allowing manufacturers to produce more units in the same time frame and meet higher market demands efficiently.
- Waste Minimization – Lower Scrap Rates and Cost Savings By optimizing process parameters, AI reduces material waste and scrap rates. This improved efficiency not only cuts down costs but also contributes to a more sustainable manufacturing operation.
- Enhanced Throughput – Increased Output Without Additional Resources Process optimization technologies allow for higher production output by eliminating bottlenecks. This increase in throughput is achieved without additional capital investment in machinery, maximizing existing resource utilization.
- Energy Efficiency – Reducing Operating Costs AI systems that monitor and optimize energy usage have demonstrated a reduction in energy consumption by up to 15%, translating into significant cost savings over the long term.
- Reduced Maintenance Costs – Lowering Operational Expenses With predictive models guiding maintenance schedules, companies experience fewer emergency repairs and less downtime, which directly reduces maintenance expenses and extends the lifespan of critical equipment.
- Improved Product Quality – Fewer Defects and Rework By ensuring that production parameters remain within optimal ranges, manufacturers see a decrease in defect rates. Improved product quality results in lower rework costs and a stronger reputation for reliability.
- Inventory Optimization – Efficient Resource Allocation AI-driven forecasting enables better inventory management, reducing the capital tied up in excess stock and minimizing storage costs. This efficiency leads to a leaner, more agile production process that is responsive to market demands.
4. Top 7 Impact Areas of AI in Supply Chain Management
- Demand Forecasting – Predicting Market Needs Accurately AI algorithms process historical sales data and external market indicators to deliver highly accurate demand forecasts. This insight ensures optimal inventory levels and minimizes the risk of stockouts or overstocking, supporting lean operations.
- Inventory Optimization – Smart Stock Management AI systems monitor real-time inventory data to maintain optimal stock levels, thus reducing both holding costs and the risk of product obsolescence. The enhanced visibility into stock movements improves order fulfillment rates.
- Route Optimization – Efficient Logistics Planning By analyzing real-time traffic data and route conditions, AI-powered logistics systems identify the fastest and most cost-effective delivery routes. This optimization reduces transit times and improves on-time delivery rates.
- Supplier Performance Management – Enhancing Vendor Reliability AI tools assess supplier performance through metrics such as delivery speed, quality, and cost efficiency. This enables manufacturers to choose and manage vendors effectively, reducing delays and ensuring a stable supply chain.
- Automated Order Processing – Accelerating the Order-to-Cash Cycle Automation in order processing minimizes manual errors and speeds up the entire cycle from order placement to cash collection. This improvement results in faster revenue recognition and improved customer satisfaction.
- Risk Management – Proactive Issue Identification AI systems identify risks such as supply chain disruptions, geopolitical instability, or natural disasters by analyzing a wide range of data sources. This proactive approach allows companies to develop contingency plans that safeguard production schedules.
- Resource Allocation – Optimizing Logistics and Distribution Centers Leveraging predictive analytics, AI determines the ideal locations for distribution centers and optimizes resource allocation across the supply chain. This strategic insight minimizes transportation costs and enhances overall efficiency.
Table: AI-Driven Manufacturing Benefits Summary
Below is a summary table that encapsulates key AI benefits in manufacturing, highlighting specific attributes and associated advantages:
AI Application | Key Benefit | Measurable Improvement | Supporting Data/Example |
---|---|---|---|
Predictive Analytics | Reduced Downtime | Up to 20% reduction in unplanned downtime | Acme Manufacturing saved 12 hours/week |
Real-Time Analytics | Immediate Process Adjustments | 15-20% cycle time reduction | Improved production flow observed |
Automated Quality Control | Enhanced Defect Detection | 90% accuracy in defect detection | Computer vision systems reduce rework |
Robotic Process Automation (RPA) | Streamlined Repetitive Tasks | Significant labor cost reduction | Workers shifted to strategic tasks |
Supply Chain Optimization | Improved Demand Forecasting | Up to 15% reduction in inventory costs | Better alignment of supply and demand |
Energy Management Systems | Reduced Operating Costs | Up to 15% energy savings | Lower energy consumption per unit produced |
Digital Twins and Process Simulation | Safe Process Testing and Training | Accelerated testing cycles | Virtual testing reduces production risks |
This table reinforces the explanation of key AI applications by providing a quick reference to their benefits. The integrated data points offer clear evidence of the measurable improvements delivered by AI solutions in the manufacturing environment.
Acme Manufacturing’s results are supported by similar quantitative outcomes reported across the industry, reinforcing the idea that AI is no longer an optional tool but a critical component of modern manufacturing strategy.
Frequently Asked Questions
Q: How can AI integration directly lead to cost savings in manufacturing? A: AI integration reduces costs by minimizing unplanned downtime, decreasing maintenance expenses, and improving resource allocation. With predictive maintenance and real-time process optimization, companies can avoid costly repairs and production halts. The automation of routine quality inspections and supply chain logistics further contributes to cost reductions by streamlining operations and lowering human error.
Q: What industries can benefit the most from AI-powered predictive maintenance? A: Industries with high-value machinery and equipment, such as automotive manufacturing, aerospace, and heavy industry, gain significant benefits from AI-powered predictive maintenance. These sectors rely on consistent operational uptime, and by predicting equipment failures before they occur, AI helps maintain continuity and prevents massive losses associated with production stoppages.
Q: How long does it typically take for a manufacturer to see the benefits of AI implementation? A: The timeline for realizing AI benefits can vary depending on the scale of implementation and operational complexity. However, many manufacturers observe noticeable improvements within three to six months as AI systems begin to optimize production processes, reduce downtime, and improve supply chain efficiency. Early pilot programs often demonstrate quick returns, which justify larger-scale deployments.
Q: What challenges are commonly faced during the transition to AI-driven manufacturing processes? A: Common challenges include integrating new AI systems with legacy technologies, ensuring data interoperability, securing staff training, and managing resistance to change. Additionally, setting up the required IT infrastructure and data collection mechanisms demands an initial investment. Overcoming these challenges requires comprehensive planning, partnerships with technology providers, and gradual scaling of AI solutions.
Moreover, organizations must also prioritize fostering a culture of innovation and adaptability among their workforce to ensure a smoother transition. This can be particularly significant during the VP’s journey to embrace AI, as leadership plays a crucial role in motivating teams and demonstrating the value of these new technologies. Engaging employees through workshops and pilot projects can also help alleviate concerns and build confidence in AI integration.
Q: Can small to mid-sized manufacturers realistically implement AI solutions? A: Yes, small to mid-sized manufacturers can implement AI solutions, often by starting with a pilot program focused on a specific area like predictive maintenance or quality control. Many AI tools are now modular and scalable, allowing companies to gradually expand their use of AI based on demonstrable cost savings and efficiency improvements. Cloud-based solutions and AI-as-a-service platforms reduce the upfront investment barrier, making it accessible to a broader range of businesses.
Q: How does AI enhance quality control compared to traditional methods? A: AI significantly accelerates quality control by employing computer vision and machine learning algorithms that detect defects faster and more accurately than manual methods. These systems continuously monitor product quality in real time and provide instant feedback, which enables immediate corrective actions and minimizes production delays. The increased consistency and reliability of automated inspections lead to higher overall product quality.
Q: What role does employee training play in the successful implementation of AI? A: Employee training is critical to the success of AI implementation because it helps bridge the gap between advanced technology and daily operations. Well-trained employees can leverage AI tools effectively, ensuring that the systems are used to their full potential for process optimization, predictive maintenance, and quality control. Ongoing training and support also help to reduce resistance to change and foster a culture of continuous improvement.
Final Thoughts
Acme Manufacturing’s journey toward reclaiming 12 hours per week through AI integration demonstrates the transformative power of technology in modern manufacturing. The strategic deployment of AI across predictive maintenance, process optimization, quality control, and supply chain management not only enhances efficiency but also delivers significant cost savings and productivity improvements. Other manufacturers can replicate these results by following a phased implementation plan and investing in robust data analytics infrastructure. The future of manufacturing lies in intelligent, people-focused AI solutions that empower businesses to work smarter and achieve sustainable growth.